A commercial warehouse plays a pivotal role in the functioning of various businesses, from retail to manufacturing, serving as storage spaces for inventory, equipment, and products. Ensuring that the roof of a warehouse remains in optimal condition is crucial for maintaining a safe and efficient operation. In this blog, we will explore the key considerations for roofing a commercial warehouse, focusing on factors that contribute to longevity, safety, and cost-efficiency. Whether you are constructing a new warehouse or maintaining an existing one, understanding these elements will help you make informed decisions that can save you money and protect your assets in the long term.
1. Understanding the Importance of Commercial Warehouse Roofing
The roof of a commercial warehouse is not just a structural element; it is a barrier protecting everything inside from external elements. Whether it’s safeguarding the products from rain or the employees from extreme temperatures, the roof is an essential part of the warehouse’s infrastructure. When roofing for commercial warehouses, the primary objectives should be durability, security, and compliance with regulations, all of which will determine the roof’s overall lifespan and performance.
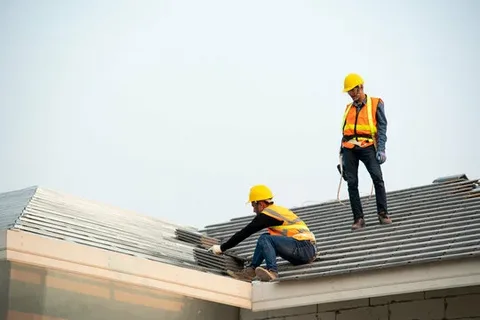
2. Material Selection for Longevity and Performance
Choosing the right material is one of the most significant considerations when it comes to roofing commercial warehouses. The roofing material you select will affect the durability, insulation, and overall cost of the project. Below are some of the most common materials used for warehouse roofs, each with its pros and cons:
- Metal Roofing: Metal is a popular choice for commercial warehouses due to its durability, fire resistance, and longevity. Steel, aluminum, and copper are some of the materials commonly used for metal roofing. A properly installed metal roof can last up to 50 years, making it an excellent long-term investment. Metal roofs are also energy-efficient, helping to regulate indoor temperatures by reflecting sunlight, which can reduce cooling costs.
- Single-Ply Membrane Roofing: Often used for flat roofs, single-ply membrane systems, such as TPO (Thermoplastic Olefin) and EPDM (Ethylene Propylene Diene Monomer), are known for their energy efficiency and low maintenance needs. These roofing systems are lightweight, resistant to UV radiation, and highly waterproof. They are a great option for warehouses in regions with harsh weather conditions.
- Built-Up Roofing (BUR): BUR roofs are composed of multiple layers of bitumen, tar, and gravel, providing exceptional waterproofing. They are ideal for areas that experience heavy rainfall or snowfall. BUR roofing is a reliable and affordable option, though it may require more maintenance than some other materials.
- Spray Foam Roofing: Spray polyurethane foam (SPF) roofs are applied directly to the existing structure, creating a seamless and highly insulative surface. SPF roofs are lightweight and can expand and contract with the building, making them ideal for warehouses in regions with fluctuating temperatures.
When selecting roofing materials for your commercial warehouse, it is essential to consider factors such as the local climate, your budget, and the building’s specific needs.
3. Roof Slope and Design Considerations
The slope of a warehouse roof plays a crucial role in water drainage. For flat or low-slope roofs, water can accumulate, leading to potential leaks and structural damage over time. To prevent this, proper slope design is essential, ensuring that rainwater flows off the roof efficiently. Typically, commercial warehouse roofs have a slope of between 1/4 inch per foot and 1/2 inch per foot, which is steep enough to prevent standing water while still being cost-effective.
In addition to slope, the design of the roof should also consider factors like:
- Ventilation: Adequate ventilation is critical to prevent heat buildup and moisture accumulation within the warehouse. Without proper ventilation, condensation can form inside the building, leading to mold growth, rusting of metal components, and damage to inventory. Ensure that your roofing system includes ventilation options like ridge vents, soffit vents, and exhaust fans.
- Accessibility: If maintenance or inspections are necessary, the roof should be accessible for workers. Proper walkways, ladders, or rooftop hatches should be incorporated into the design to ensure safety during regular maintenance.
- Expansion Needs: Consider whether the warehouse will need to be expanded in the future. Designing a roofing system with expansion in mind can help you avoid the cost of retrofitting later.
4. Insulation for Energy Efficiency
Proper insulation is one of the most important factors to consider when roofing a commercial warehouse. Insulating the roof not only helps maintain a comfortable environment inside the warehouse but also contributes to significant cost savings. Well-insulated roofs reduce the need for excessive heating or cooling, leading to lower energy bills.
In addition to cost savings, insulation helps in:
- Temperature Regulation: In warehouses that store temperature-sensitive goods, such as food or chemicals, temperature control is essential. Insulation can help regulate internal temperatures, reducing the load on HVAC systems and improving overall energy efficiency.
- Condensation Control: Insulation can help reduce the potential for condensation on the underside of the roof, which can damage inventory, equipment, and the building itself.
- Noise Reduction: Insulated roofs also help reduce noise from external sources, such as rain or hail, making the indoor environment more conducive to work.
5. Roof Maintenance and Inspections
Regular maintenance is crucial to extend the lifespan of a warehouse roof. Without proper care, even the highest-quality roofing material can become susceptible to damage. Establishing a proactive maintenance schedule is the best way to prevent costly repairs and ensure the roof’s performance over time.
Routine maintenance should include:
- Cleaning Gutters and Drains: Clear any debris from gutters and drains regularly to prevent water from pooling on the roof. Clogged drains can lead to roof leaks and structural damage.
- Inspecting for Leaks and Damage: Regular inspections will help detect any early signs of leaks, cracks, or other issues that could lead to costly repairs down the line.
- Checking Flashings and Seals: Ensure that roof flashing, seals around vents, and skylights remain intact. Any gaps or cracks in these areas can allow water to infiltrate, leading to damage.
- Re-coating or Sealing: Over time, the roof’s protective coating may wear down. Depending on the material, applying a new layer of sealant or protective coating can help maintain the roof’s waterproofing and energy efficiency.
6. Roofing Safety Considerations
Safety should be a top priority during both the installation and maintenance of a warehouse roof. Commercial roofs can be hazardous environments, especially if they are steep or lack proper fall protection.
Key safety considerations include:
- Training and Equipment: Ensure that all workers are properly trained in rooftop safety, including how to use fall protection equipment, ladders, and harnesses. Using the correct safety gear, including hard hats, safety ropes, and guardrails, is essential to prevent accidents.
- Weather Conditions: Always schedule roof work during favorable weather conditions. Avoid roofing projects during heavy rain, strong winds, or extreme temperatures, as these can increase the risk of accidents.
- Structural Integrity: Ensure that the roof structure is capable of supporting the weight of workers, materials, and equipment. If the roof is old or has sustained damage, it may require reinforcement before workers can safely access it.
7. Choosing the Right Roofing Contractor
Selecting an experienced and reliable roofing contractor is crucial to ensure the quality and safety of your commercial warehouse roof. When hiring a contractor, consider the following:
- Experience and Reputation: Look for contractors with a proven track record of working on commercial warehouse roofs. Check their references and online reviews to gauge their reputation.
- Licensing and Insurance: Ensure that the contractor is licensed and carries the necessary insurance to protect both you and their workers during the roofing process.
- Warranty and Maintenance Plans: A good roofing contractor will offer a warranty on both materials and labor, as well as options for ongoing maintenance.
Conclusion
The roof of your commercial warehouse plays a crucial role in maintaining the safety, longevity, and efficiency of your business operations. By considering factors such as material selection, insulation, roof slope, and regular maintenance, you can ensure that your warehouse roof provides maximum protection and minimizes long-term costs.
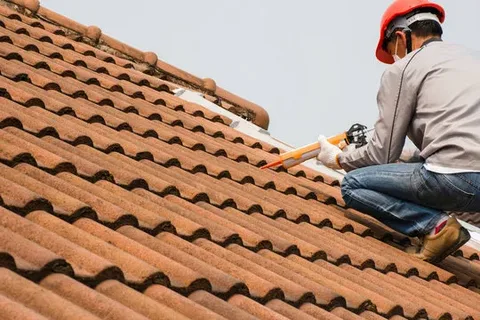
At Atlas Roofing & Restoration, we specialize in commercial roofing services for warehouses and other commercial properties. Our team of experienced professionals is dedicated to delivering high-quality roofing solutions that are built to last. If you’re looking to ensure the safety, efficiency, and longevity of your warehouse roof, trust Atlas Roofing & Restoration to provide expert service and top-notch materials. Reach out today for an inspection or consultation.